變速器齒輪經常在高轉速、高負荷、轉速和負荷不斷交變的情況下工作,根據其工作環境而要求其表面強度硬度高、心部韌性好,故基本采用滲氮或碳氮共滲處理。變速器齒輪在滲碳淬火過程中始終伴隨著產品變形,控制產品熱處理的變形量一直是熱處理工作者探索的目標。在實際生產中,目前主要是依靠加大熱處理后產品的磨削余量,以消除熱處理對產品尺寸的影響,提高產品的精度。由于熱處理后產品變形不一致,齒輪在磨削過程中同一齒面的不同部位磨削量不一致,導致磨削后齒面滲層深淺不一,特別是齒面的殘余應力分布不均勻,影響齒輪的使用壽命,增加了齒輪的生產成本,降低生產效率。
本文試驗產品為主減速齒輪,產品規格如下圖1所示。其材料選用20CrMoH、17CrNiMo6、TL4521三種牌號進行試驗,從工藝、合金元素、毛坯組織及擺料方式四方面進行試驗分析對變形的影響。
1.熱處理工藝對變速箱齒輪變形的影響
熱處理變形主要體現在加熱與淬火過程中,淬火變形起主導作用,淬火時在工件中引起的內應力是造成變形的根本原因,當內應力超過材料的屈服強度極限強度時便引起工件變形,淬火變形有兩種主要的形式:一種是工件幾何形狀的變化,它表現為尺寸及外形的變化,通常稱為扭曲或翹曲,另一種是體積變化,表現為工件體積按比例脹大或收縮。在主減速齒輪熱處理加熱與淬火中,主減速齒輪變形往往是幾何形狀變化與體積變化的相互疊加。熱處理工藝上可通過增加預熱、降低淬火溫度、合理選擇淬火冷卻介質與滲碳層深度減少變形量,其原始工藝如圖2a所示,改進后工藝如圖2b所示。
增加預熱工序,可減少加熱時表面與心部的溫度差,心部與表面溫差大,會導致心部與表面漲縮不同時性而存在應力,當應力超過材料組織屈服強度極限,便會引起加熱過程中熱應力引起的變形。降低淬火溫度與選擇合理的淬火冷卻介質均可以降低淬火由于高溫快速冷到低溫熱應力引起的收縮變形。
從圖2a、2b兩種工藝可知:TL4521熱處理工藝改進的主要有:滲碳加熱790℃預熱30min,縮小加熱過程中表面與心部的溫度差;預冷淬火溫度從820℃降低到TL4521材料淬火溫度的極限值790℃,保存產品合格的前提下減小產品淬火熱應力,降低主減速從動齒輪淬火變形;淬火油由科潤等溫淬火油K468C改為科潤等溫淬火油K498C,K498C冷卻速度比K468C慢,使用溫度比K468C高,產品在采用K468C等溫淬火油的冷卻過程中可減小工件表面與心部馬氏體轉變的不同時性。
從圖3不同熱處理工藝生產的產品心部組織可知,圖2a工藝1生產的產品(見圖3a)心部組織為板條馬氏體+少量的粒狀貝氏體(5%的含量),心部硬度為45HRC,采用圖2b工藝2生產的產品心部組織為板條馬氏體+粒狀貝氏體(35%的含量),心部硬度為41HRC。圖2工藝1與工藝2生產的產品表面硬度,心部硬度,有效硬化層等均合格,圖2工藝2生產的產品心部組織粒狀貝氏體較多,粒狀貝氏體的比容比板條馬氏體的比容小,有利于減小產品滲碳淬火過程中的組織應力。
根據表1中TL4521熱處理工藝1與TL4521熱處理工藝2的平放變形量對比,改進后的工藝2在內孔與端面跳動方面均有一定的改善,減小了產品的變形量。
表1 TL4521不同熱處理工藝熱處理(平放)后變形量(mm)
2.合金元素對齒輪變形的影響
齒輪材料加熱保溫奧氏體化,合金元素融入奧氏體中,C曲線右移動,增加奧氏體的穩定性,提高了材料的淬透性。而合金元素(Al、Co除外)與碳原子強烈的降低了材料的MS點,合金元素越高,材料的Ms點降低,若Ms點較低,則開始發生馬氏體轉變時工件的溫度較低,在相同滲碳淬火溫度情況下,淬火溫度至Ms點的溫差較大,故合金元素的提高會加大了產品的淬火熱應力變形,且隨著奧氏體溶解的合金元素增加,淬火馬氏體比容越大,組織應力略微增大。不同合金元素對Ms點的影響為:Mn>Cr>Ni>Mo。
表2 不同材料的合金元素含量(質量分數)(%)
從表2可知,材料中合金元素含量:17CrNiMo6>TL4521>20CrMoH;從表3熱處理變形數據可以看出,同工藝與裝爐方式熱處理的主減速變形量:17CrNiMo6>TL4521>20CrMoH。
表3 三種材料主減速平放變形數據(mm)
3.毛坯組織對變速箱齒輪變形的影響
齒輪毛坯一般要求采用等溫正火工藝,不允許有混晶,魏氏體組織≤1級,帶狀≤3級,組織為等軸狀鐵素體與珠光體,不允許有粒狀貝氏體組織等(如圖4a正常毛坯組織)。齒坯預備熱處理組織的均勻性和穩定性對齒輪最終熱處理變形的影響很大, 因為齒輪各部分的原始組織不同, 組織一致性差, 在熱處理加熱至奧氏體狀態后存在成分的不均勻,因而可能影響淬火后的組織不均勻,即那些低碳低合金元素區域可能得不到馬氏體(而得到的是屈氏體或貝氏體),或者得到比容比較小的低碳馬氏體,從而將造成工件不均勻的變形。
毛坯組織中容易混雜粒狀貝氏體(如圖4f異常毛坯組織),粒狀貝氏體產生是由于熱處理正火冷卻速度過快,奧氏體轉變為貝氏體,貝氏體為非平衡組織,在直接滲碳加熱奧氏體化過程中容易導致組織遺傳,使得奧氏體晶粒粗大,晶粒粗大的產品在受力變形時,晶界位錯堆積比較嚴重,易產生裂紋,會降低齒輪的疲勞壽命。其次貝氏體硬度比平衡組織高,熱前機加工困難,加工切削過程留下的殘余應力較大,殘余應力在滲碳加熱過程中釋放,加大產品熱處理變形量。
表4 TL4521不同毛坯組織平放熱處理后變形量(mm)
從毛坯組織圖(見圖4)和不同毛坯組織堆放熱后變形量(見表4)可得:毛坯組織對變速箱齒輪變形影響很大,粒貝與偏析加大產品熱后變形量,TL4521來料粒貝毛坯熱處理后變形量是TL4521來料正常毛坯的3倍。
4.裝爐方式對變速箱齒輪變形的影響
變速箱主減速從動齒輪裝爐方式主要有三種:平放、豎放、堆放(見圖5)。不同的裝爐方式,工件在加熱過程受力不同,掛放受自身重力的作用,相對平放,內孔可能較容易產生橢圓,堆放變速箱主減速從動齒輪受多個工件直接的作用力,相對而言產品的跨棒距略微增加。不同的裝爐方式,主減速在淬火冷卻過程入油的阻力大小與冷卻的均勻性均不同。
表5 TL4521材料產品不同裝爐方式后變形量(mm)
從表5不同裝爐方式變形數據測量表明:平放的熱后端跳>豎放熱后端跳>堆放熱后端跳,平放的內孔收縮最大,堆放的內孔收縮最小,但堆放與平放的內孔橢圓度均較大,主要是由于豎放在加熱過程中由于自重的影響而導致橢圓度增大,堆放是由于冷卻過程不一致而導致內孔橢圓度較大。同時堆放主減速齒輪外端面冷卻快,內端面冷卻慢,控制內外端面的冷卻速度,使得熱后內孔收縮量大幅度減少。
5.討論與分析
熱處理應變有尺寸變化和形狀變化,通常尺寸變化時由組織變化引起的,即由相變引起的膨脹和收縮造成的,形狀變化主要是由于零件的自重引起的下垂和由應力引起的形狀走樣。熱處理應變的出現涉及三個階段:加熱(基于內應力的消除),保溫(自重下垂,即下垂彎曲),冷卻(基于不均勻的冷卻和相變),這三個互相疊加最終導致零件的淬火應變。
本文通過增加預熱工序減少熱處理過程中加熱引起的形狀變化,降低淬火溫度與選用粘度大冷速更慢些的淬火油KR498C,增加粒狀貝氏體含量,減少奧氏體轉變為馬氏體比容的變化而引起的尺寸變化與熱應力引起的形狀變化;合理的要求毛坯組織來料,控制毛坯中貝氏體含量與帶狀等級,從而降低因毛坯來料組織不均勻而加重熱處理過程中產品的尺寸變化;根據主減速產品尺寸結構,通過選擇堆放主減速使齒輪外端面冷卻快,內端面冷卻慢,控制內外端面的冷卻速度,從而熱處理后內孔收縮量大幅度減少。
6.結語
(1)毛坯組織對變速箱齒輪變形影響很大,粒貝與偏析加大產品熱后變形量,TL4521來料粒貝毛坯熱處理后變形量是TL4521來料正常毛坯的3倍。
(2)主減速齒輪采用堆放的裝爐方式比掛放與平放的裝爐方式端面跳動略微降低,內孔收縮明顯減小。
(3)TL4521材料的淬火溫度從820℃降低至790℃,熱處理后主減速產品的心部產生粒狀貝氏體,尺寸變化和形狀變化均減小,從而減小變形。
本文試驗產品為主減速齒輪,產品規格如下圖1所示。其材料選用20CrMoH、17CrNiMo6、TL4521三種牌號進行試驗,從工藝、合金元素、毛坯組織及擺料方式四方面進行試驗分析對變形的影響。
1.熱處理工藝對變速箱齒輪變形的影響
熱處理變形主要體現在加熱與淬火過程中,淬火變形起主導作用,淬火時在工件中引起的內應力是造成變形的根本原因,當內應力超過材料的屈服強度極限強度時便引起工件變形,淬火變形有兩種主要的形式:一種是工件幾何形狀的變化,它表現為尺寸及外形的變化,通常稱為扭曲或翹曲,另一種是體積變化,表現為工件體積按比例脹大或收縮。在主減速齒輪熱處理加熱與淬火中,主減速齒輪變形往往是幾何形狀變化與體積變化的相互疊加。熱處理工藝上可通過增加預熱、降低淬火溫度、合理選擇淬火冷卻介質與滲碳層深度減少變形量,其原始工藝如圖2a所示,改進后工藝如圖2b所示。
增加預熱工序,可減少加熱時表面與心部的溫度差,心部與表面溫差大,會導致心部與表面漲縮不同時性而存在應力,當應力超過材料組織屈服強度極限,便會引起加熱過程中熱應力引起的變形。降低淬火溫度與選擇合理的淬火冷卻介質均可以降低淬火由于高溫快速冷到低溫熱應力引起的收縮變形。
從圖2a、2b兩種工藝可知:TL4521熱處理工藝改進的主要有:滲碳加熱790℃預熱30min,縮小加熱過程中表面與心部的溫度差;預冷淬火溫度從820℃降低到TL4521材料淬火溫度的極限值790℃,保存產品合格的前提下減小產品淬火熱應力,降低主減速從動齒輪淬火變形;淬火油由科潤等溫淬火油K468C改為科潤等溫淬火油K498C,K498C冷卻速度比K468C慢,使用溫度比K468C高,產品在采用K468C等溫淬火油的冷卻過程中可減小工件表面與心部馬氏體轉變的不同時性。
從圖3不同熱處理工藝生產的產品心部組織可知,圖2a工藝1生產的產品(見圖3a)心部組織為板條馬氏體+少量的粒狀貝氏體(5%的含量),心部硬度為45HRC,采用圖2b工藝2生產的產品心部組織為板條馬氏體+粒狀貝氏體(35%的含量),心部硬度為41HRC。圖2工藝1與工藝2生產的產品表面硬度,心部硬度,有效硬化層等均合格,圖2工藝2生產的產品心部組織粒狀貝氏體較多,粒狀貝氏體的比容比板條馬氏體的比容小,有利于減小產品滲碳淬火過程中的組織應力。
根據表1中TL4521熱處理工藝1與TL4521熱處理工藝2的平放變形量對比,改進后的工藝2在內孔與端面跳動方面均有一定的改善,減小了產品的變形量。
表1 TL4521不同熱處理工藝熱處理(平放)后變形量(mm)
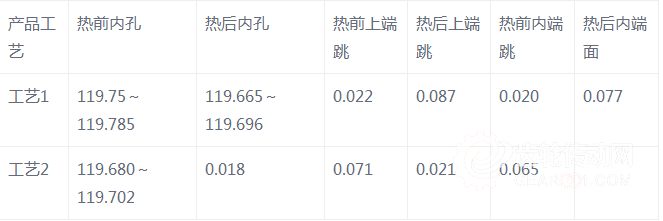
2.合金元素對齒輪變形的影響
齒輪材料加熱保溫奧氏體化,合金元素融入奧氏體中,C曲線右移動,增加奧氏體的穩定性,提高了材料的淬透性。而合金元素(Al、Co除外)與碳原子強烈的降低了材料的MS點,合金元素越高,材料的Ms點降低,若Ms點較低,則開始發生馬氏體轉變時工件的溫度較低,在相同滲碳淬火溫度情況下,淬火溫度至Ms點的溫差較大,故合金元素的提高會加大了產品的淬火熱應力變形,且隨著奧氏體溶解的合金元素增加,淬火馬氏體比容越大,組織應力略微增大。不同合金元素對Ms點的影響為:Mn>Cr>Ni>Mo。
表2 不同材料的合金元素含量(質量分數)(%)

從表2可知,材料中合金元素含量:17CrNiMo6>TL4521>20CrMoH;從表3熱處理變形數據可以看出,同工藝與裝爐方式熱處理的主減速變形量:17CrNiMo6>TL4521>20CrMoH。
表3 三種材料主減速平放變形數據(mm)

3.毛坯組織對變速箱齒輪變形的影響
齒輪毛坯一般要求采用等溫正火工藝,不允許有混晶,魏氏體組織≤1級,帶狀≤3級,組織為等軸狀鐵素體與珠光體,不允許有粒狀貝氏體組織等(如圖4a正常毛坯組織)。齒坯預備熱處理組織的均勻性和穩定性對齒輪最終熱處理變形的影響很大, 因為齒輪各部分的原始組織不同, 組織一致性差, 在熱處理加熱至奧氏體狀態后存在成分的不均勻,因而可能影響淬火后的組織不均勻,即那些低碳低合金元素區域可能得不到馬氏體(而得到的是屈氏體或貝氏體),或者得到比容比較小的低碳馬氏體,從而將造成工件不均勻的變形。
毛坯組織中容易混雜粒狀貝氏體(如圖4f異常毛坯組織),粒狀貝氏體產生是由于熱處理正火冷卻速度過快,奧氏體轉變為貝氏體,貝氏體為非平衡組織,在直接滲碳加熱奧氏體化過程中容易導致組織遺傳,使得奧氏體晶粒粗大,晶粒粗大的產品在受力變形時,晶界位錯堆積比較嚴重,易產生裂紋,會降低齒輪的疲勞壽命。其次貝氏體硬度比平衡組織高,熱前機加工困難,加工切削過程留下的殘余應力較大,殘余應力在滲碳加熱過程中釋放,加大產品熱處理變形量。
表4 TL4521不同毛坯組織平放熱處理后變形量(mm)
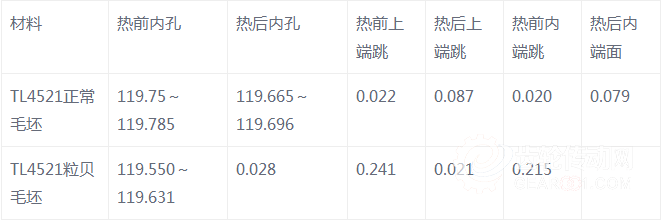
從毛坯組織圖(見圖4)和不同毛坯組織堆放熱后變形量(見表4)可得:毛坯組織對變速箱齒輪變形影響很大,粒貝與偏析加大產品熱后變形量,TL4521來料粒貝毛坯熱處理后變形量是TL4521來料正常毛坯的3倍。
4.裝爐方式對變速箱齒輪變形的影響
變速箱主減速從動齒輪裝爐方式主要有三種:平放、豎放、堆放(見圖5)。不同的裝爐方式,工件在加熱過程受力不同,掛放受自身重力的作用,相對平放,內孔可能較容易產生橢圓,堆放變速箱主減速從動齒輪受多個工件直接的作用力,相對而言產品的跨棒距略微增加。不同的裝爐方式,主減速在淬火冷卻過程入油的阻力大小與冷卻的均勻性均不同。
表5 TL4521材料產品不同裝爐方式后變形量(mm)
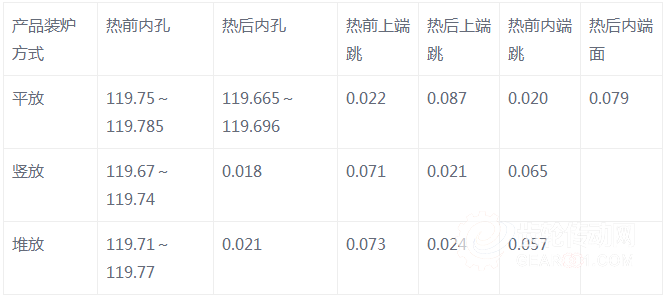
從表5不同裝爐方式變形數據測量表明:平放的熱后端跳>豎放熱后端跳>堆放熱后端跳,平放的內孔收縮最大,堆放的內孔收縮最小,但堆放與平放的內孔橢圓度均較大,主要是由于豎放在加熱過程中由于自重的影響而導致橢圓度增大,堆放是由于冷卻過程不一致而導致內孔橢圓度較大。同時堆放主減速齒輪外端面冷卻快,內端面冷卻慢,控制內外端面的冷卻速度,使得熱后內孔收縮量大幅度減少。
5.討論與分析
熱處理應變有尺寸變化和形狀變化,通常尺寸變化時由組織變化引起的,即由相變引起的膨脹和收縮造成的,形狀變化主要是由于零件的自重引起的下垂和由應力引起的形狀走樣。熱處理應變的出現涉及三個階段:加熱(基于內應力的消除),保溫(自重下垂,即下垂彎曲),冷卻(基于不均勻的冷卻和相變),這三個互相疊加最終導致零件的淬火應變。
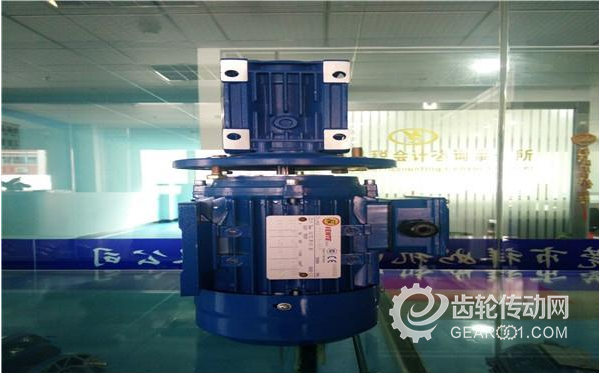
本文通過增加預熱工序減少熱處理過程中加熱引起的形狀變化,降低淬火溫度與選用粘度大冷速更慢些的淬火油KR498C,增加粒狀貝氏體含量,減少奧氏體轉變為馬氏體比容的變化而引起的尺寸變化與熱應力引起的形狀變化;合理的要求毛坯組織來料,控制毛坯中貝氏體含量與帶狀等級,從而降低因毛坯來料組織不均勻而加重熱處理過程中產品的尺寸變化;根據主減速產品尺寸結構,通過選擇堆放主減速使齒輪外端面冷卻快,內端面冷卻慢,控制內外端面的冷卻速度,從而熱處理后內孔收縮量大幅度減少。
6.結語
(1)毛坯組織對變速箱齒輪變形影響很大,粒貝與偏析加大產品熱后變形量,TL4521來料粒貝毛坯熱處理后變形量是TL4521來料正常毛坯的3倍。
(2)主減速齒輪采用堆放的裝爐方式比掛放與平放的裝爐方式端面跳動略微降低,內孔收縮明顯減小。
(3)TL4521材料的淬火溫度從820℃降低至790℃,熱處理后主減速產品的心部產生粒狀貝氏體,尺寸變化和形狀變化均減小,從而減小變形。