近年來,隨著國防軍工、航空航天、生物工程和醫療器械等高端技術領域需求的快速增長,機械制造業正朝著精密化、微細化、柔性化以及智能化方向發展,這對加工制造的水平提出了更高要求。集機、光、電、控制等多學科融合的超精密微細加工技術代表了加工制造的最高水準,其不僅與國防工業和高新技術的發展密切相關,還決定了國家在激烈國際競爭中的話語權,因此,世界各國對此都十分重視。
超精密微細加工技術的進步很大程度上依賴機床行業的發展,經過三十多年,我國機床行業已具備相當規模,但國內機床產業大而不強,機床產品主要集中在低、中端領域,高檔數控機床產品仍主要依賴進口,競爭力相對較低,尤其是作為國家戰略制造裝備的超精密加工機床的技術水平十分薄弱。《中國制造2025》將高檔數控機床提升到需要大力發展的戰略高度。
機床被譽為“工業母機”,是整個裝備制造業生產的核心基礎。超精密加工機床科技含量和精密程度高,在精密微小復雜自由曲面加工方面具有顯著優勢。雖然國內很多機床企業也能生產五軸聯動機床,但核心部件仍需外購,在眾多核心技術領域仍是空白。
制約我國機床水平提高的因素有很多,一是基礎科學方面,材料性能不達標,生產工藝不完善,結構設計不合理,使得零部件性能達不到要求,可靠性差;二是控制、測量技術方面,國內現有的機床運動模型與機床系統的兼容性、通用性差,傳感器靈敏度低,測量裝置精度低,限制了機床自身的精度。攻克高端數控機床的“卡脖子”技術、徹底解決核心技術的“阿喀琉斯之踵”是我國機床行業乃至整個制造業由大變強的必經之路。
2 超精密加工機床
目前將加工精度0.1~0.01μm、加工表面粗糙度0.04~0.005μm的加工稱為超精密加工。超精密加工機床是實現超精密加工的首要基礎條件,而超精密機床的精度指標尚無統一標準,工業界達成的共識是參照20世紀90年代由美國Union Carbide公司、Moore公司和美國空軍兵器研究所等制定的“POMA”計劃,將進給分辨率達到0.005μm、主軸回轉精度達到0.02μm、定位精度達到0.05μm、直線度精度達到0.02μm、綜合精度達到0.1μm的機床稱為超精密加工機床。
從國家戰略的角度來看,掌握超精密加工核心技術能引領高端加工制造業的發展,并在激烈的國際競爭中取得先機。因此世界各國從上世紀開始紛紛布局,制定戰略來重點發展超精密加工技術,如上世紀50年代開始,美國出于在航天、國防等領域發展需求,率先開始超精密加工技術的研究,20世紀80年代,美國軍方制定了“先進制造技術開發計劃”,英國先后制定了“NION國家納米技術計劃”、“LINK納米計劃”,日本制訂了“ERATO先進技術探索研究計劃”等。美、英、日、德、瑞士等國家對超精密加工技術研發的持續投入也加速了其在民用領域的產業化進程,上世紀80年代開始,美國的摩爾(Moore)、普瑞斯泰克(Precitech),日本的芝浦(Shibaura)、發那科(Fanuc),德國吉德曼(Gildemeister)等企業陸續推出了超精密加工機床,并開始投入民用產品制造,逐步實現了超精密加工機床的商品化,但在這一時期大部分超精密加工機床為專用機床。從90年代開始,超精密加工機床的核心技術(例如檢測系統、控制系統、驅動系統、精密導軌與軸承等)已逐漸發展成熟,并且汽車、相機、光學儀器等商品的普及極大提高了人們對超精密加工技術的需求,從而促使超精密加工機床成為民品領域較為常見的加工設備。
1980年,美國摩爾(Moore)公司開發的M-18AG型超精密非球面加工車床引領超精密加工技術進入亞微米級,該機床采用氣浮導軌、空氣靜壓軸承、空氣隔振彈性支承以及優質鑄鐵床身,并配備雙頻雙坐標激光測量系統及恒溫系統,使得加工精度可達0.3μm,加工直線度可達0.5nm/mm,加工表面粗糙度低至7.5nm。隨后該公司先后推出了以Nanotech 250UPL、350UPL、500FG為代表的超精密加工設備,其中,三軸超精密加工機床Nanotech 250UPL(見圖1a)采用模塊化設計,可以將B旋轉軸和Y直線軸進行拆卸更換,其X,Z直線軸行程為200mm,回轉半徑最大可達125mm,通過配備超精密伺服車削系統,使得最小分辨率達到0.01nm,加工表面粗糙度小于2nm,面形精度小于0.1μm;五軸數控機床Nanotech 350FG可以進行超精密磨削和單點金剛石車削,其直線軸采用液體靜壓導軌,穩定性高,使得直線軸最小分辨率達到0.034nm,重復定位精度300nm,主軸徑向和軸向跳動量小于13nm,重復定位精度±1arc/s,如圖1所示。
為滿足國防需求,從20世紀60年代起,美國開始了超精密加工機床的研究歷程,美國勞倫茲實驗室(LLNL)先后開發了DTM-1、DTM-2超精密加工機床,并于1983年成功研制出DTM-3臥式大型超精密光學加工車床,其刀架采用摩擦驅動,配備液體靜壓導軌和軸承,并搭載激光干涉儀,使得加工精度可達13nm,加工表面粗糙度達到7.6nm。

圖1 Nanotech 系列超精密加工機床
20世紀80年代,美國率先開始進行激光核聚變研究,為制造超大型激光器(NIF)所需的大口徑光學元件,美國國防部投資1300萬美元成功研制出大型光學元件超精密金剛石切削車床LODTM,其加工直徑可達Φ1.625m,如圖2所示,該機床具備快速電致伸縮微進給裝置(FTS)、激光在線測量系統、空氣隔振系統和超高精度溫度控制系統,在1.6m的加工范圍內徑向加工誤差28nm,直線度誤差小于0.025μm,加工表面圓度和平面度小于12.5nm,加工表面粗糙度小于4.2nm,代表了超精密加工的最高水平。

圖2 LODTM立式大型光學金剛石車床
英國Cranfield精密工程研究所(CUPE)是歐洲超精密加工高水平的代表,也是世界精密工程研究中心之一,其在1991年為加工X射線太空望遠鏡鏡筒而研制的OAGM2500大型六軸數控超精密磨床(見圖3)配備了精密數控驅動系統和雙頻激光測量系統,該系統X,Y軸最大行程為2500mm,Z軸最大行程為610mm,X,Y軸配備液體靜壓軸承,Z軸和專用探測頭采用空氣軸承,平面加工精度可達1μm,加工表面粗糙度可達2nm。為了滿足車削和研磨的使用要求,CUPE于1991年又成功研制出Nanocentre250、Nanocentre600等多款非球面零件超精密加工機床,該系列機床通過配備高剛度的液體靜壓軸承和伺服驅動系統,最小分辨率可達1.25nm,加工表面粗糙度小于10nm,面形精度小于0.1μm。

圖3 OAGM2500大型超精密磨床
美、英研制的DTM-3、LODTM和OAGM2500三臺機床代表了超精密加工的世界最高水平。相較于美、英等國,日本的超精密加工技術起步較晚,但發展迅猛,其發展路徑與美、英相比明顯不同,日本超精密加工的研究主要針對民用產品,如精密測量儀器、醫療器械、微電子以及光學元件等,這種研究方向也決定了日本的超精密加工機床具有小而精的特點。20世紀90年代,日本東芝機械成功研制的ULG-100A(H)超精密非球面復合加工機床,通過同時控制兩個旋轉軸(刀具軸和工件軸)可以實現非球面光學透鏡模具的切削和磨削加工,其X軸(刀具軸)最大行程150mm,Z軸(工件軸)最大行程100mm,由于配備了空氣靜壓軸承和高精度位置反饋光柵,使得旋轉軸分辨率可達10nm。豐田工機研制的具有車、磨復合加工功能的AHN05、AHN10、AHN60-3D等超精密加工機床可以實現3D自由曲面的超精密切削、磨削加工,通過配備無鐵心直線電機、頻閃儀、亞微米精度光柵等,使得加工表面粗糙度可達16nm,表面精度可達0.35μm。
除美、英、日外,德國、瑞士等國家在超精密加工領域也在不斷加大投入,均進入了世界第一梯隊。
3 超精密加工機床典型結構
超精密加工機床的類別與普通機床相似,可以從不同角度進行劃分:按照通用程度可劃分為通用型和專用型,如普通超精密加工車床、磁盤超精密加工車床等;按照加工工藝方法可分為超精密加工車床、超精密加工銑床、超精密加工磨床、超精密拋光機床以及超精密復合加工中心等;按照設備的復雜程度,超精密加工機床可以從兩軸擴展到五軸。
3.1 兩軸聯動超精密加工機床
兩軸聯動超精密加工機床是結構最簡單的超精密加工機床,如臥式超精密車床、超精密飛切機床等。圖4為Precitech公司研制的Nanoform L1000兩軸聯動超精密車床。

圖4 Nanoform L1000兩軸聯動超精密車床
其X,Z直線軸呈T形安置在機床底座上,主軸布置在X軸導軌上,刀具則布置在Z軸導軌上,在X,Z直線軸的相互配合下,同時在主軸的旋轉帶動下,利用高精度圓弧刃金剛石刀具可實現非球面曲面等回轉類零件的超精密加工,該機床直線軸采用靜壓油軸承導軌,配合對稱的直線電機布置,可實現0.01nm的編程分辨率,其加工表面粗糙度<1.25nm,形狀精度<0.125μm。
用于大口徑KDP晶體拋光的超精密單點金剛石飛切機床是一種可實現納米級超精密切削加工的兩軸聯動超精密加工機床。哈爾濱工業大學研制的超精密單點金剛石飛切機床的結構如圖5所示,在進行飛切加工時,工件固定在工作臺上,通過調節Y軸預先設定好切削深度,Z軸以低速緩慢進給的方式移動,主軸驅動飛切盤從而帶動刀具對工件進行切削加工。所有運動軸均采用空氣靜壓軸承支撐,直線軸采用直線電機,旋轉主軸采用力矩電機直接驅動,運動精度極高,機床床身配備空氣彈簧,可以對環境振動等干擾進行有效控制。該機床可以直接將光學晶體、有色金屬等材料加工到鏡面水平,適用于光學零件的大批量生產。
3.2 三軸聯動超精密加工機床
三軸聯動超精密加工機床最基本的特征是有且只有三個運動軸可以實現聯動控制。三個聯動軸可能是X,Y,Z三個直線軸的組合,也可能是旋轉軸和直線軸的組合。如美國Moore公司研制的Nanotech 350UPM高效超精密微磨削/微銑削機床(見圖6),X,Y,Z三個直線軸均采用全約束箱式油靜壓軸承滑軌,Y軸(垂直軸)采用雙線性電機驅動并配備空氣軸承自適應平衡器用于優化伺服性能,所配置的空氣軸承磨削主軸轉速可達60000r/min(配有液體致冷),編程分辨率可達0.01nm,該機床適用于對非球面曲面和微溝槽等結構進行微細銑削加工,可以得到傳統機床無法達到的光學表面精度和粗糙度。

圖5 超精密單點金剛石飛切機床
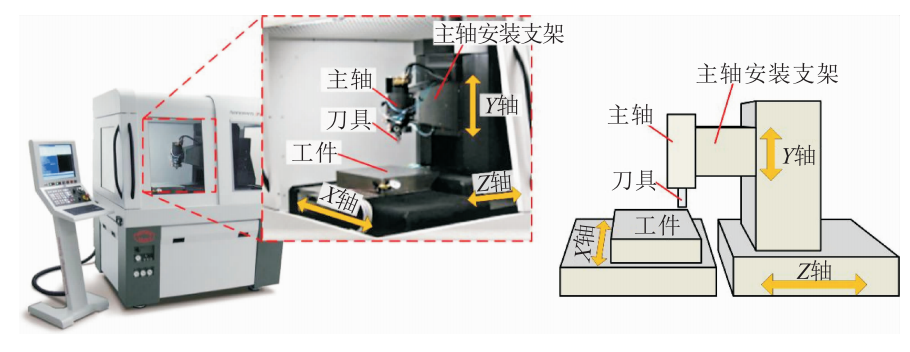
圖6 Nanotech 350UPM三軸聯動超精密機床
圖7為一種包括2個直線軸和1個旋轉軸的三軸聯動超精密車床,該機床的旋轉軸采用雙驅模式,既可作為普通旋轉主軸進行速度閉環控制,又可作為角度伺服軸進行角度位置閉環控制。
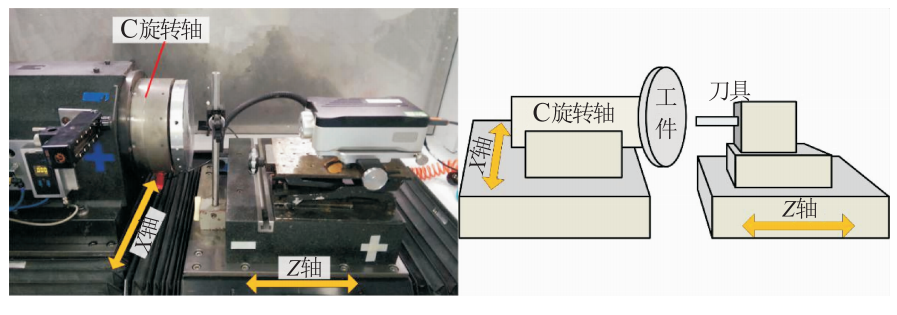
圖7 X,Z,C三軸聯動超精密車床
3.3 四軸聯動超精密加工機床
四軸聯動超精密加工機床通常是在三軸聯動超精密加工機床的基礎上增加一個聯動軸擴展的超精密加工設備。為滿足不同產品的加工技術要求,生產廠商通過產品的模塊化結構設計,發展同系列和跨系列變形品種,從而衍生出不同結構的多軸超精密加工機床。如Moore公司研制的Nanotech 450UPL系列超精密加工機床,通過改變模塊化結構,可以適應各種球面和非球面部件的加工,通過增添可拆卸Y軸模塊形成了X,Y,Z,C結構的四軸聯動超精密加工機床(見圖8b);通過增添B旋轉軸模塊、主軸單元等,形成了X,Z,B,C結構四軸聯動超精密加工機床(見圖8c)。
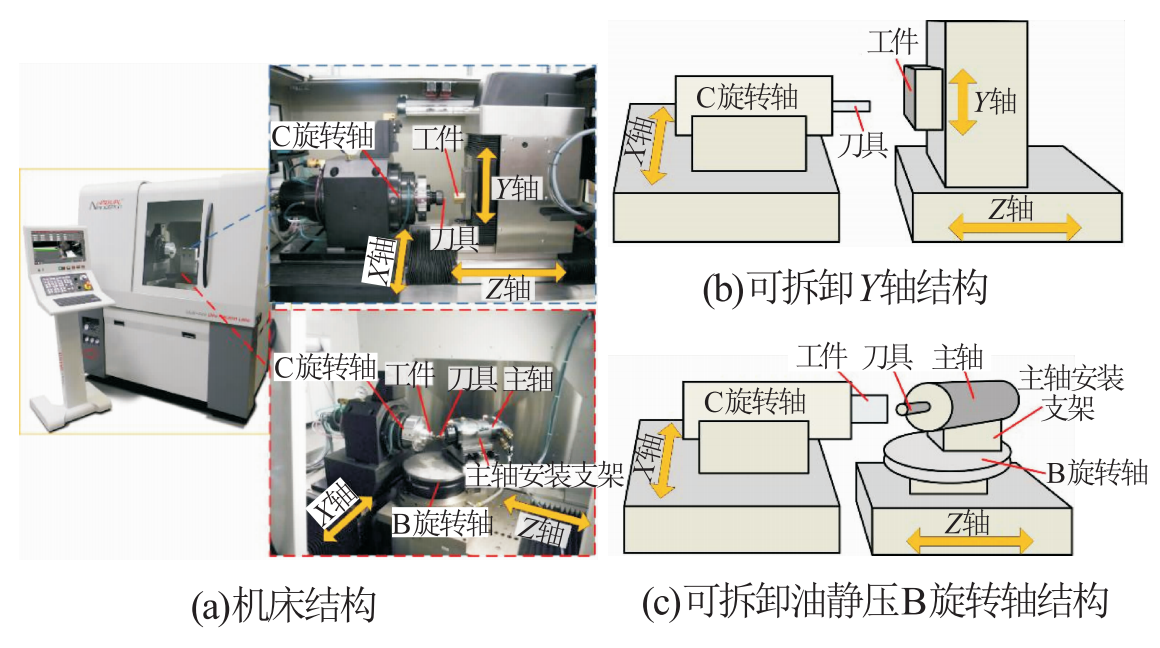
圖8 Moore Nanotech 450UPL超精密加工機床
機床所有運動軸均采用全約束油靜壓閉式導軌,主軸采用多孔石墨空氣靜壓軸承,由無刷直流電機驅動,最大轉速為10000r/min,軸向/徑向運動精度可達12.5nm。機床線性分辨率可達0.01nm,角度分辨率可達(0.1×10-7)°,其加工表面粗糙度可達納米級,輪廓精度達到亞微米級。
3.4 五軸聯動超精密加工機床
五軸聯動超精密加工機床是在三軸聯動超精密加工機床的基礎上,通過增加兩個聯動軸來實現自由曲面高精加工。2001年,瑞士米克朗公司推出的HSM400U高速五軸聯動加工中心(見圖9)在漢諾威EMO機床展上正式亮相,成為世界上第一臺真正的五軸聯動超精密加工機床。此后的二十年間,為適應不同的市場需求,各種五軸聯動超精密加工機床被相繼開發。
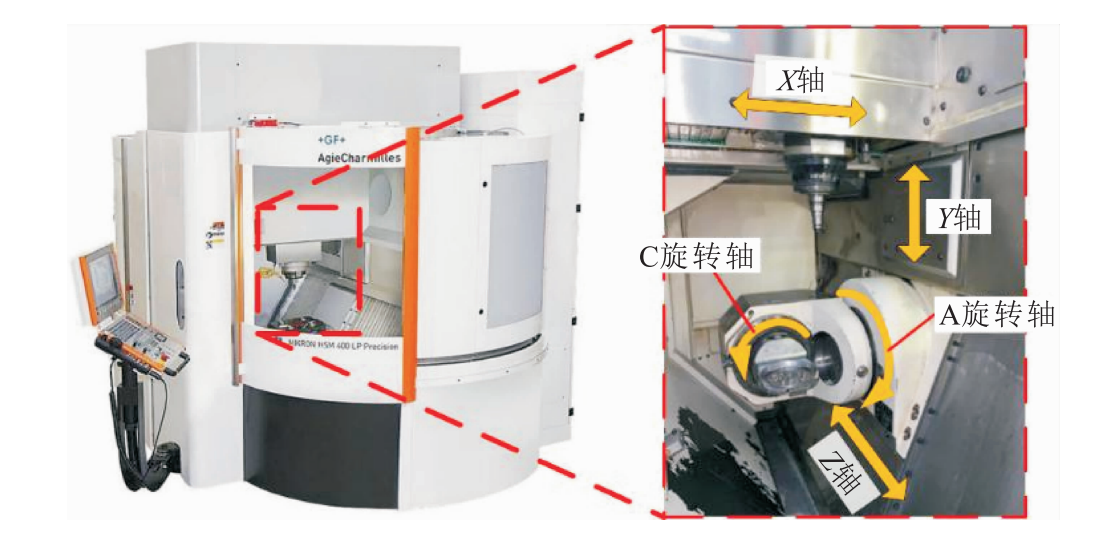
圖9 HSM400U五軸聯動超精密加工機床
目前,市場上主流的五軸聯動超精密加工機床包括3個平動軸(T)與2個旋轉軸(R)的組合,根據旋轉軸在機床中的布局,五軸超精密加工機床可分為三個基本類型(見圖10)。其中,單擺頭—單轉臺結構(RTTTR)中,一個旋轉軸(擺動軸)在主軸端,一個旋轉軸(回轉軸)在工作臺端,由于兩個旋轉軸分別在機床的兩條運動鏈上,因此工作臺剛度較好,尺寸無限制,適用于加工小型零件,多應用于中、小型五軸超精密加工機床上。
圖10a為FANUC Robonano α-0iB RTTTR型五軸超精密加工機床,其所有的運動軸均采用空氣靜壓軸承,直線軸采用直線電機驅動,旋轉軸采用內裝伺服電機驅動,能夠實現1nm的步進分辨率。雙轉臺結構(RRTTT)機床的兩個旋轉軸均在工作臺一端,也稱為“搖籃式”結構,如圖10b所示,該結構機床主軸剛性較好,加工效率高,與單擺頭—單轉臺結構相比,在相同的行程內加工范圍更大,但由于需要實現工作臺擺動,所以其負重往往有嚴格的限制,多用于加工中、小型零件,如中小型葉片、渦輪等。雙擺頭結構(TTTRR)的五軸超精密加工機床如圖10c所示,兩個旋轉軸均位于主軸端,由于雙擺頭自身尺寸較大,考慮加工范圍的需要,一般會做成龍門式,因此該結構更適合加工大型零部件,如機身、機翼等。

圖10 五軸聯動超精密加工機床典型結構
3.5 超精密加工機床關鍵零部件
不同種類的超精密加工機床雖然結構有所差異,但功能部件基本相同,包括旋轉軸、平動軸、主軸單元、切削刀具、工作臺及機床床身等,其中,旋轉軸、主軸單元和切削刀具是對超精密微細自由曲面加工影響最大的關鍵零部件。
旋轉軸是多軸超精密加工機床的重要組成部分,其運動精度對非自由曲面的加工精度影響較大。增加旋轉軸使得機床在靈活性和高效性方面具有明顯優勢,但引入旋轉軸使機床的機械結構更為復雜。目前,超精密加工機床旋轉軸系統常采用液體或氣體等流體介質懸浮軸承,減振性好且磨損小,但剛度較差,運動精度更易受到GEs、FIEs、熱誘導誤差、加工顫振等因素的影響。
主軸單元是超精密加工機床的關鍵部件之一,按照動力來源主要分為以下兩種:
一種是電主軸,受散熱條件、穩定性等多種因素的限制,目前商業化的電主軸轉速大部分在50000~150000r/min,個別達到300000r/min。如Moore公司推出的Nanotech系列超精密加工機床,以無刷直流電機驅動,采用多孔質材料節流氣體靜壓軸承,最高轉速可達60000r/min,回轉精度小于12.5nm。廣州昊志機電股份有限公司的DQF-400氣體靜壓電主軸,最高轉速可達400000r/min,回轉精度小于2μm,主要用于PCB轉孔加工。
另一種是氣動渦輪主軸。如FANUC公司推出的Robonano系列五軸聯動超精密加工機床,采用空氣靜壓軸承氣動渦輪主軸,其最高轉速可達60000r/min,回轉精度約為0.05μm。Precitech公司的Nanoform系列超精密加工機床采用氣動渦輪主軸,其最高轉速可達80000r/min,回轉精度小于0.03μm。采用氣流驅動與空氣軸承支承的渦輪式主軸受益于氣體低溫升、低摩擦系數和高流速,主軸轉子可達到極高的回轉速度,但隨著轉速升高,跳動誤差也會不斷增大。此外,靜壓承載力、轉子質量、流體均勻性等對氣浮渦輪主軸的承載性能和回轉精度都會產生影響。
微細刀具是超精密微細加工中剛性最薄弱的環節,其尺寸大小、幾何結構、材料性能等對加工尺寸、切削質量和加工精度都有很大影響。微細刀具尺寸決定了加工零件尺度,通常微細刀具的直徑小于1mm,如果微細刀具的直徑能進一步減小,則微型零件尺寸也必將減小,甚至能逼近蝕刻技術所能加工的尺度。目前,通過聚焦離子束加工技術,可以加工出直徑小于50μm的微型立銑刀。然而,在微細加工中,所設定的每齒進給量可能小于刀具刃口半徑以及刀具—刀架—主軸系統的跳動量,受尺寸效應、未變形切削厚度、微尺度材料性能等因素影響,微細加工機理與傳統加工之間存在較大差異。在超精密微細加工過程中,微細刀具與加工工件直接接觸,微細刀具的這些特性會導致加工過程的穩定性較差,從而出現較大的加工誤差。
為滿足柔性化的加工需求,許多超精密加工機床都進行了模塊化設計,為便于機床在不同模塊之間相互切換,設計出許多專用連接裝置,例如圖6、圖8c、圖10a所示的主軸安裝支架,極大提高了主軸拆卸、更換的便利性。該類連接裝置提高機床整體靈活性的同時,也會改變機床結構的剛度,引入裝配誤差,從而影響機床的加工性能。
總體來說,超精密加工機床的零部件制造精度、裝配工藝水平等已經達到了目前技術的最高水平,從理論上講,若能準確、有效地控制這些機床關鍵零部件所產生的誤差,將進一步提升超精密加工機床的加工精度。
我國從上世紀50年代就開始了針對超精密加工技術的研究,但在70年代后才重視其發展。1958年,上海機床廠自主研制出我國第一臺高精度磨床,一舉打破國際壟斷;1987年,北京機床研究所成功研制出能夠進行球面加工的空氣軸承主軸超精密加工車床,然后又成功研制出超精密加工銑床和超精密數控車床,提升了我國超精密加工的水平。但這一時期,我國仍沒有開發出能夠進行非球面加工的超精密加工機床,與國外相比還存在較大的差距。“九五”期間,北京機床研究所研制的NAM-800納米級超精密數控車床的反饋系統分辨率達到2.5nm,機械進給系統可實現5nm的微進給,使得直線軸直線度達到0.15μm/200mm,主軸回轉精度達到30nm,加工表面粗糙度達到8nm。同時,哈爾濱工業大學、國防科技大學、北京航空精密機械研究所等高校、科研機構在超精密加工技術領域也在不斷取得進步。
4 超精密加工機床發展趨勢
超精密加工機床作為國家重要的戰略物資,已經成為體現一個國家制造業最高水準的代表之一,發展趨勢如下:
(1)高效、精密
高精度與高效率是機械加工所追求的兩大目標。當前,超精密復合加工技術,如化學機械拋光、磁流變拋光等,雖能加工出具有極高表面完整性和表面質量的工件,但耗時長、加工效率低。而高速車削、銑削加工技術雖然加工效率高,但無法獲得上述復合加工工藝所能達到的加工精度。探索高效加工基礎上的誤差補償與控制技術以及高精加工基礎上的高效加工技術,進而開發出全新的超精密加工設備成為超精密加工領域的研究目標。
(2)智能化、無人化
智能制造是制造業未來發展的主流方向,通過提高加工設備的智能化水平可以降低對人工經驗的依賴,甚至完全代替人工,這也是制造業不斷追求的目標。智能制造依賴于人工智能、類腦技術等新興技術領域的發展,智能網絡技術、實時在線監測診斷技術等是未來智能化加工機床必須具備的核心技術,也是提高產品質量和生產效率的重要保障。
(3)復合式、通用化
在激烈的市場競爭中,高效生產已經成為企業的生命線。在此背景下,諸如“以銑代磨”、“以磨代研”以及“以磨代拋”等跨等級加工工藝的需求不斷提高,此外,能夠同時具備車、銑、刨、磨等功能的通用復合式機床成為市場研發的重要方向。
(4)極大化、極小化
為滿足航空航天、武器裝備等領域所需大型光學器件等的加工要求,需要研發大型超精密加工設備。同時,為滿足微型電子機械、光電信息等領域所需微型器件(如微型傳感器、微型驅動元件)的加工需求,需要研發微型超精密加工設備(并非加工微小型工件一定需要微小型加工設備)。因此,超精密加工設備需要向大型化、微型化兩極發展。
(5)綠色節能
“碳中和”、“碳達峰”是提高我國經濟全球競爭力的重要戰略,也是我國對世界的承諾。加快降低碳排放步伐,探索高效節能的新型加工方式、降低切削液的使用、提高材料利用率、引導綠色技術創新是制造業的發展趨勢。
5 結語
超精密加工技術已經滲入人們生活各方面,鑒于軍事、信息等產業對高精度零部件件的巨大需求,我國超精密加工機床雖已取得長足的進步,但與生產實際要求相比,與國外還有一定差距,這一局面在短期內仍無法改變,因此我國應加大對超精密加工機床研究的持續投入,不斷進行知識技術儲備,力爭打破高端超精密加工設備被國外壟斷的局面。